En théorie, il existe déjà la norme CSA A277 – Mode opératoire visant la certification des bâtiments, des modules et des panneaux préfabriqués, qui garantit une certaine qualité d’exécution. Cette norme demande aux industriels d’établir un programme de qualité de tous leurs produits, et les usines sont auditées pour vérifier leur programme. « Chaque unité qui sort de l’usine a une étiquette qui certifie sa conformité, et le programme de qualité doit être audité et approuvé. Ce programme vient rassurer les architectes et les autorités compétentes », décrit Martin Lagacé.
Encore faut-il que ce programme réponde aux exigences des architectes et qu’il documente les détails qui intéressent l’architecte. Martin Lagacé préconise d’adapter le programme pour inclure, par exemple, des photos de détails, des maquettes 3D. « Ajouter des étapes d’inspection pour assurer le bon passage entre le manufacturier et le chantier va faciliter le partage des responsabilités », croit-il.
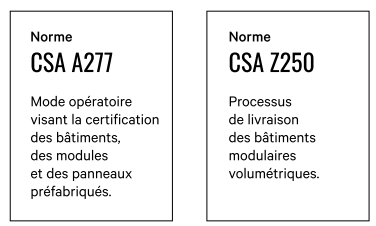
Mais comme la norme CSA A277 se concentre sur les procédés de fabrication, elle ne lève pas toutes les ambiguïtés. « Comment on gère le transport, l’arrivée sur le chantier des éléments préfabriqués, leur manipulation et leur assemblage pour livrer un bâtiment conforme ? » questionne Martin Lagacé. C’est l’objet de la norme CSA Z250 – Processus de livraison des bâtiments modulaires volumétriques, publiée en 2021, et qui standardise le contrôle de qualité des étapes de construction en dehors de l’usine. Elle définit la logistique de transport, d’entreposage et de manutention des unités préfabriquées ; l’installation, la finition et la mise en service jusqu’au processus d’approbation des bâtiments préfabriqués. Et elle demande l’établissement d’une matrice de responsabilités. Ces matrices sont déjà en usage chez RG Solution.
Martin Lagacé en explique le principe. « Quand on réalise un projet, on s’assoit avec tous les intervenants, architectes, ingénieurs, entrepreneur général, et nous comme manufacturier. Pour chaque élément, on fait une matrice de l’ensemble des étapes de fabrication et de construction. On précise qui intervient à chaque étape et quelles sont ses responsabilités. » Le manufacturier peut notifier dans la matrice des détails d’assemblage à l’intention du constructeur. Par exemple, lors de la fabrication en usine, RG Solution prévoit un débordement du pare-vapeur pour la jonction intermodulaire, mais pour utiliser à bon escient ces débordements, le constructeur doit en être informé. « Créer une matrice et l’appuyer avec des informations techniques spécifiques aux étapes critiques permet de faire le passage entre les différents intervenants et d’assurer une continuité dans la responsabilité des étapes et de l’imputabilité de tous les partis », avance Martin Lagacé.
La norme CSA Z250 ne fait pas tout. Elle a le potentiel de dissiper le flou de la responsabilité, à condition de bien communiquer. « Ce n’est pas parce que l’information est disponible qu’elle est nécessairement bien comprise par tous, observe Martin Lagacé. Il faut que les intervenants puissent se parler pour s’assurer que tout est clair. »