Un virage s’impose
L’application des stratégies et technologies de l’industrialisation au domaine du bâtiment est réclamée depuis de multiples décades, surtout pour l’habitation. Il y a un siècle (1920), Le Corbusier proposait d’industrialiser sa « Maison Citrohan » à la manière d’une auto « Citroën » !
Ce sont maintenant les économistes qui réagissent à l’inefficacité de la construction traditionnelle comparativement à la productivité des autres domaines. Ils le font en réclamant l’industrialisation du bâtiment tout en recourant à des termes analogues tels que production de masse, préfabrication, construction hors site, modularisation, etc.
Dans un article publié le 17 août 2017 et intitulé « The construction industry’s productivity problem », le magazine The Economist est explicite : « […] no industry has done worse… But the trade as a whole is reluctant to spend money on the sorts of technologies, from project-management software to mass production, that have revolutionised so many other industries1 ».
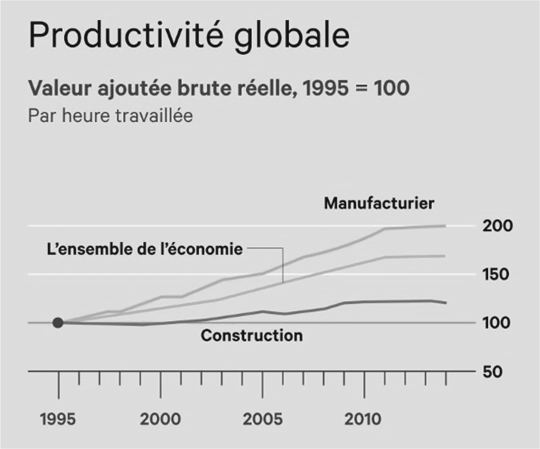
Productivité des secteurs manufacturier et construction. – Source : The Economist, 17 août 2017.
L’Institut McKinsey Global abonde dans le même sens dans un rapport intitulé Tackling the world’s affordable housing challenge diffusé le 1er octobre 2014 : « Project costs could be reduced by about 30 percent and completion schedules shortened by about 40 percent if developers make use of value engineering (standardizing design) and industrial approaches, such as assembling buildings from prefabricated components manufactured off-site2. »
Publié en juin 2020, son autre rapport, The next normal in construction: How disruption is reshaping the world’s largest ecosystem, annonce que l’approche service (project based) est en voie d’être détrônée par l’approche produit préusiné :
Today’s construction ecosystem
The construction process is highly project based – developed from unique customer specifications, using designs planned from scratch, and with limited degree of repetition. The value chain and player landscape are local and highly fragmented vertically and horizontally, resulting in a multitude of players involved at each step and major interface frictions. Construction is performed by generalists on site in hostile environments, with a large part of the workforce being temporary and manual.
The construction ecosystem of the future
The construction process is increasingly product based, meaning structures will be products and manufactured off-site by branded product houses specializing in certain end-user segments. Developers choose entire designs or specific components from a library of options developed in-house or offered externally on the market3.
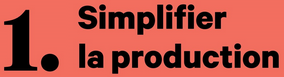
Le premier principe gouvernant les stratégies opère à la façon d’une équation : recruter la quantité afin d’amortir des technologies en mesure de simplifier la production tout en offrant une qualité de haut niveau.
Simplifier la production est le principe de base de l’industrialisation. Mais cela n’est pas nécessairement le cas avec la « préfabrication » (c.-à-d. d’avance) ou la construction off-site (c.-à-d. ailleurs), car les méthodes y sont souvent quasi identiques à celles du chantier malgré l’accès à un outillage plus élaboré à l’abri des contingences climatiques. Le fait de transférer les opérations manuelles de la préfabrication à des outillages recourant à l’automation ou à la robotique ne va pas simplifier la production pour autant. Ce sont les procédés dits de « reproduction » qui vont le faire, en introduisant des technologies innovantes capables de court-circuiter les opérations à caractère répétitif (Richard, 2005).
Quelques stratégies de reproduction sont déjà présentes dans le domaine du bâtiment : les matériaux à multiple rendement, tel le béton cellulaire ; les outils livrant un composant complexe en une seule opération, telle l’extrusion des profilés de mur-rideau ; de même que les facilitateurs de jointement, tels les connecteurs d’acier multidirectionnels. Mais il faut aller encore beaucoup plus loin.
L’approche DfMA (Design for Manufacturing and Assembly)
C’est en vue de simplifier la production que les divers manufacturiers de plusieurs de plusieurs régions du globe (Allemagne, Royaume-Uni, Sud-Est asiatique, et al.) adoptent actuellement l’approche DfMA : « DfMA is an engineering methodology that focuses on simplifying the design of a product to improve ease of manufacture and efficiency of assembly » (Siemens, 2020)4.
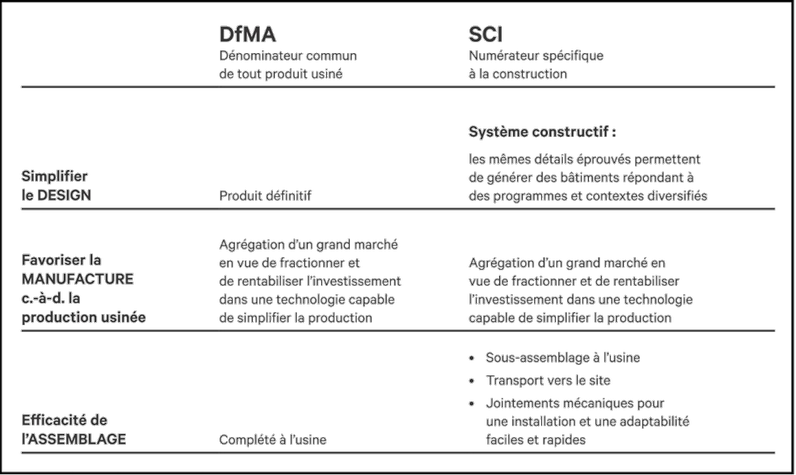
Le DfMA devient en quelque sorte un dénominateur commun où les systèmes constructifs industrialisés (SCI) se positionnent comme numérateur affichant des propriétés qui leur sont propres :
• Le Design architectural vise l’individualisation et l’adaptabilité aux changements.
• Le Manufacturing partage l’objectif commun de simplifier la production.
• L'Assembly a lieu sur un site géographiquement éloigné de l'usine. lieu sur un site géographiquement éloigné de l’usine.
Encore faut-il que les entreprises transfèrent dans les prix sur le marché la réduction des coûts engendrée par cette approche !
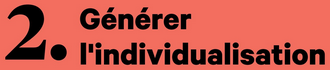
Spectaculaire paradoxe ! L’amortissement des technologies capables de simplifier la production implique un minimum de détails et de procédés normalisés, mais ne signifie pas la standardisation des bâtiments, bien au contraire.
Le second principe regroupe quatre stratégies de production en mesure de générer l’individualisation, c’est-à-dire pouvant livrer un produit individualisé répondant aux spécificités des occupants dans l’espace et le temps : flexibilité du produit, flexibilité de l’outil, polyvalence et combinatoire (Richard, 2011).
Chacune de ces quatre stratégies constitue un clavier distinct, mais complémentaire aux trois autres. L’ensemble peut donc couvrir presque toutes les spécificités des occupants.
a. Flexibilité du produit
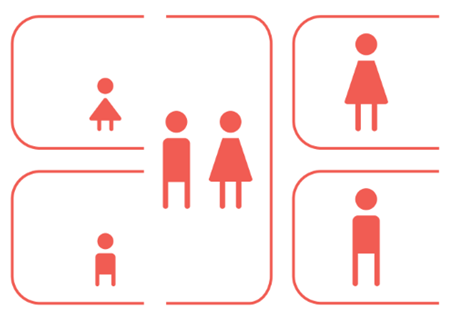
Évolution de la relation parents - enfants- adolescents.
Facilité de relocaliser un composant standardisé afin de répondre facilement aux changements. Comme lors des changements liés à l’évolution de la relation parents-enfants-adolescents, où une proximité visuelle est nécessaire en bas âge, mais contestée à l’adolescence ! Les options les plus évidentes sont les modules de rangement linéaire ainsi que la cloison amovible légère fixée par pression à sa base.
b. Flexibilité de l'outil
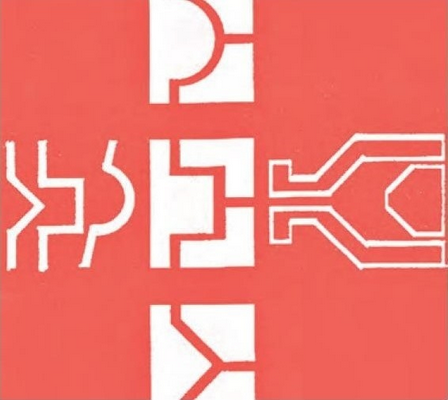
Intervention mécanique / extraction numérique / addition numérique.
Le procédé en tant que tel devient générateur de produits différents :
• Par intervention mécanique, c’est-à-dire changement de matrice / permutation de gabarit ou de moule.
• Par extraction numérique, c’est-à-dire fraisage.
• Par addition numérique, c’est-à-dire impression 3D et Contour Crafting (Khoshnevis, 2003).
c. Combinatoire
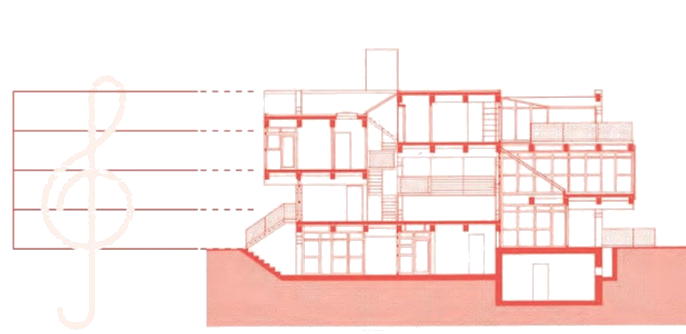
Analogie musique et projet Genterstrasse de l'architecte Oto Steidle.
La combinatoire implique la conception d’un nombre minimal de composants destinés à être produits en grande série et à permettre une multiplicité de variations lors de l’assemblage. La musique en offre une analogie éloquente : sept notes standardisées utilisées à des millions d’exemplaires sur la grille modulaire qu’est la portée sont à la base de toutes les œuvres que nous connaissons. C’est ainsi que les différentes typologies du projet Genterstrasse à Munich sont générées par seulement trois composants standardisés : une seule colonne type (avec console à chaque demi-étage), une seule poutre type et une seule poutrelle type.
d. Polyvalence
La polyvalence implique une structure d’accueil normalisée, ouverte à une diversité de compléments. C’est le cas de la « plateforme » chez les manufacturiers automobiles et de l’ossature aux arêtes chez les principaux manufacturiers de modules volumétriques japonais.

Structure d'accueil et éléments détachables de l'approche Open Building tel qu'appliquée par l'Urban Angency – UR au Japon et adaptabilité de l'édifice Next21 réalisé à l'initiative d'Osaka Gas.
L’approche Open Building en est l’archétype : la structure d’accueil (support) standardisée permet l’insertion d’éléments détachables (infill) à relocaliser en fonction des intentions de l’occupant (Habraken, 1976). NEXT21 à Osaka, l’édifice multilogement le plus adaptable au monde, applique intégralement cette approche (Yositika Utida, architecte en chef).
Il en va de même pour la structure d’accueil en bois d’ingénierie de l’édifice BSH20A Stories récemment réalisé à Amsterdam.
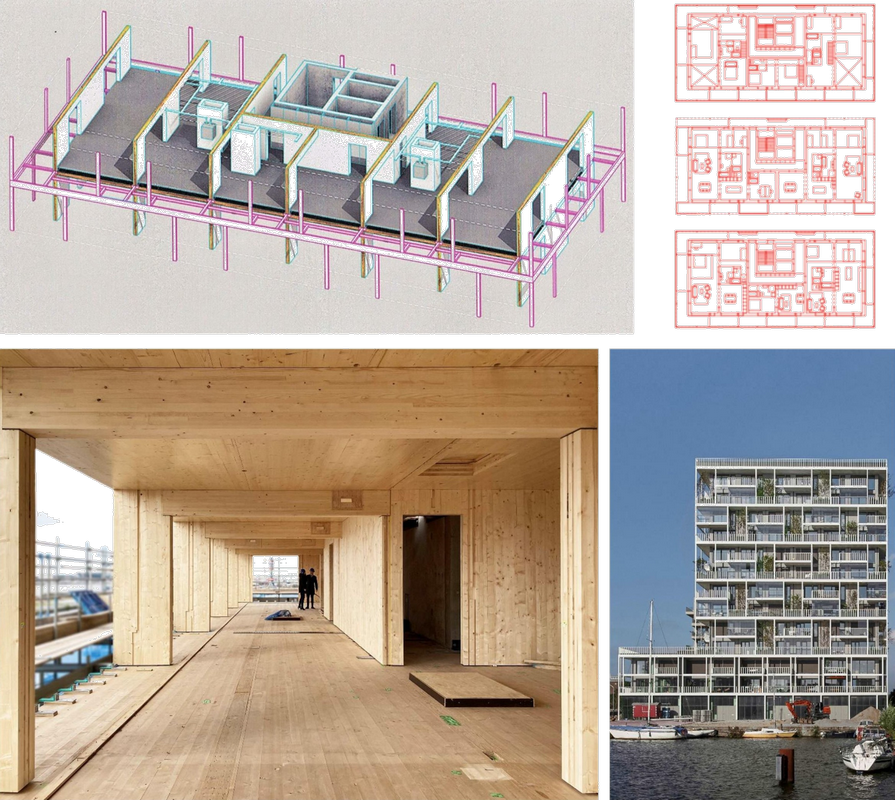
Structure d’accueil en bois d’ingénierie de l’édifice BSH20A Stories à Amsterdam et adaptabilité des logements, Olaf Gipser Architects.
Le produit de l’industrialisation du bâtiment n’est généralement pas un bâtiment fini, mais plutôt un système constructif industrialisé (SCI) : un ensemble d’outils et de composants où les mêmes procédés et détails éprouvés sont configurés de façon à générer de multiples variations correspondant aux spécificités des occupants.
L’application des SCI interpelle les manufacturiers pour l’ensemble des sous-systèmes en limitant le rôle des entrepreneurs généraux, à l’inverse de la situation actuelle où la compétition ne se fait pas à armes égales :
• Le manufacturier doit s’engager dans des investissements majeurs en outillage avant même de livrer un tout premier produit bâtiment ou sous-système et d’atteindre éventuellement le seuil de rentabilité ;
• L’entrepreneur général n’a pas à investir pour offrir ses services et réaliser quelque projet que ce soit. Il n’a qu’à souscrire à une caution financière. Il va réunir une équipe de sous-traitants et engager la main-d’œuvre uniquement pour la durée du chantier dans la plupart des cas, tout en évitant des déboursés à moyen ou long terme grâce aux paiements progressifs du client.
Par ailleurs, rien n’empêche les entrepreneurs généraux de s’allier avec des manufacturiers ou de devenir eux-mêmes manufacturiers, comme c’est le cas de plusieurs grandes entreprises en Asie du Sud-Est.
Rôle prédominant des sous-systèmes
L’efficacité d’un système constructif est tributaire de l’interaction des cinq fonctions principales du bâtiment que sont les sous-systèmes : la charpente, l’enveloppe, le cloisonnement, les services et les équipements. Chaque sous-système répond à des critères de rendement distincts et nécessite une technologie spécialisée, bien que certains sous-systèmes gagnent parfois à être intégrés.
La « Palette » des options
Il n’y a pas de meilleur SCI au monde que des systèmes appropriés à des contextes spécifiques. Le niveau de partage des sous-systèmes entre l’usine et le site du projet va définir trois grandes catégories de systèmes : le Meccano assemblé au chantier, le volume usiné et l’hybride.
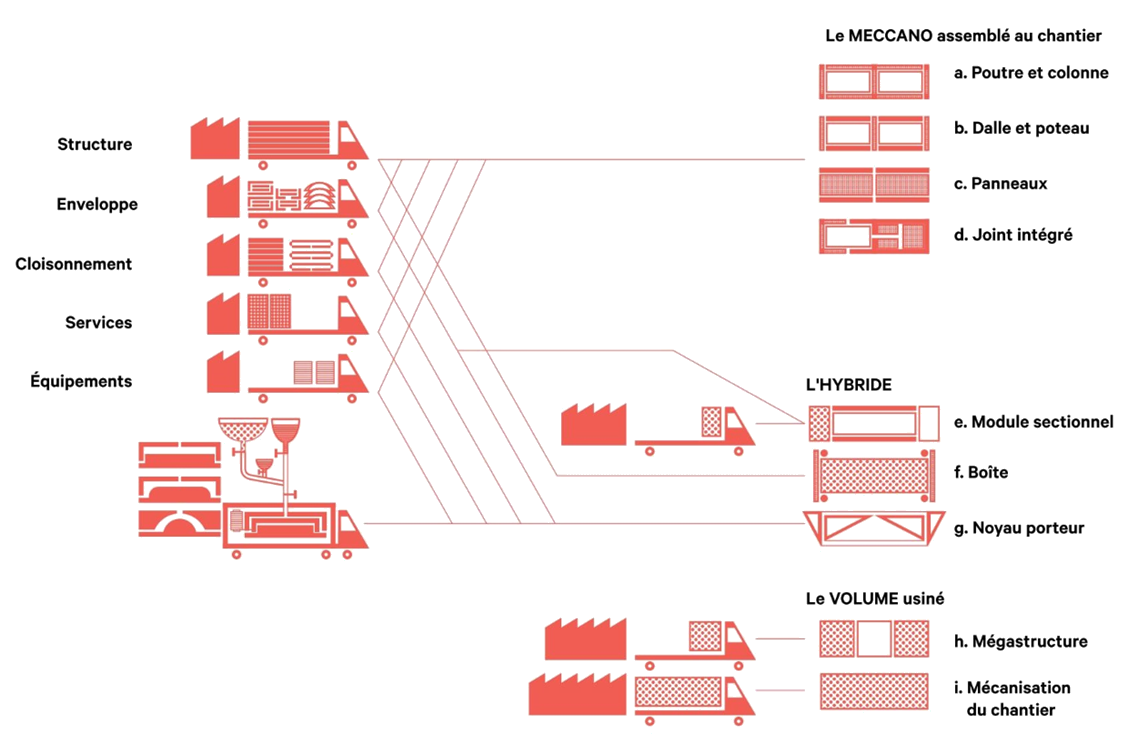
Interaction sous-systèmes et systèmes constructifs.
Regroupés à l’intérieur de ces trois catégories, neuf types de systèmes constituent l’essentiel d’une « palette » permettant aux décideurs de sélectionner la technologie optimale pour un contexte donné (Richard, 2017).
Un dixième type couvre les « sous-systèmes ouverts », dont le rôle principal est de compléter certains systèmes qui, pour des raisons diverses, n’incluent pas tous les sous-systèmes.
Dans le cadre du présent article, seuls quelques exemples seront présentés ; même si chaque type offre généralement plusieurs variantes et plusieurs options en ce qui concerne les principaux matériaux que sont le bois, le métal et le béton.
I. Le Meccano assemblé au chantier – Environ 60 à 65 % du travail est réalisé en usine
Les sous-systèmes sont produits en usines spécialisées, puis transportés au chantier en pièces détachées.
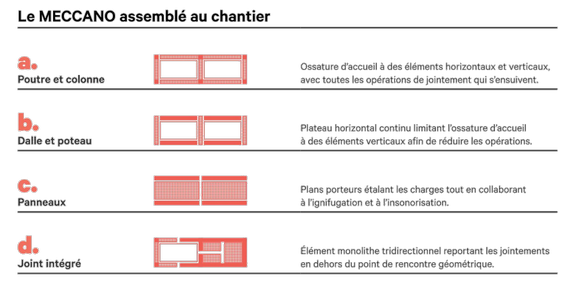
Les quatre type de Meccano assemblés au chantier
Même si l’industrialisation vise à maximiser la production effectuée en usine, il ne faut pas rejeter d’emblée les systèmes qui impliquent un montage élaboré au chantier, à la condition que leurs jointements y soient faciles et rapides à exécuter.
a. Poutre et colonne
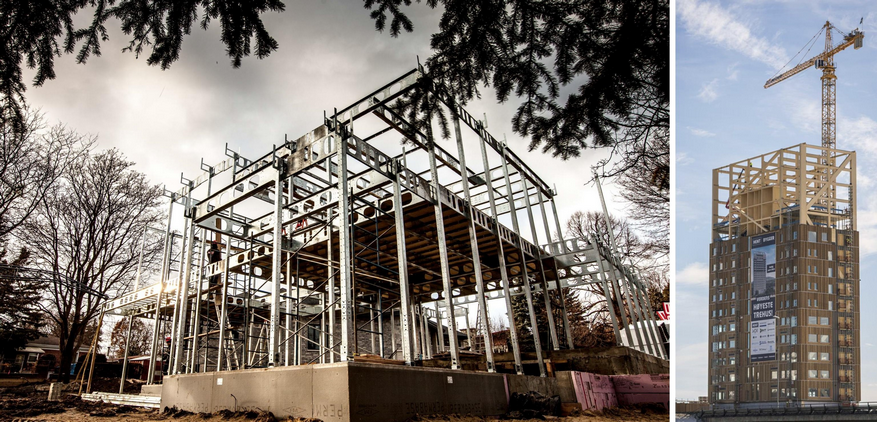
La poutre et colonne offre le maximum de souplesse sur tous les axes, car la charpente équivaut à un squelette ouvert à l’insertion d’éléments diversifiés. Le système québécois BONE Structure en présente les avantages à l’échelle résidentielle unifamiliale, alors que l’édifice Mjostarnet fait de même pour un projet multifonctionnel de 18 étages en bois d’ingénierie.
b. Dalle et poteau
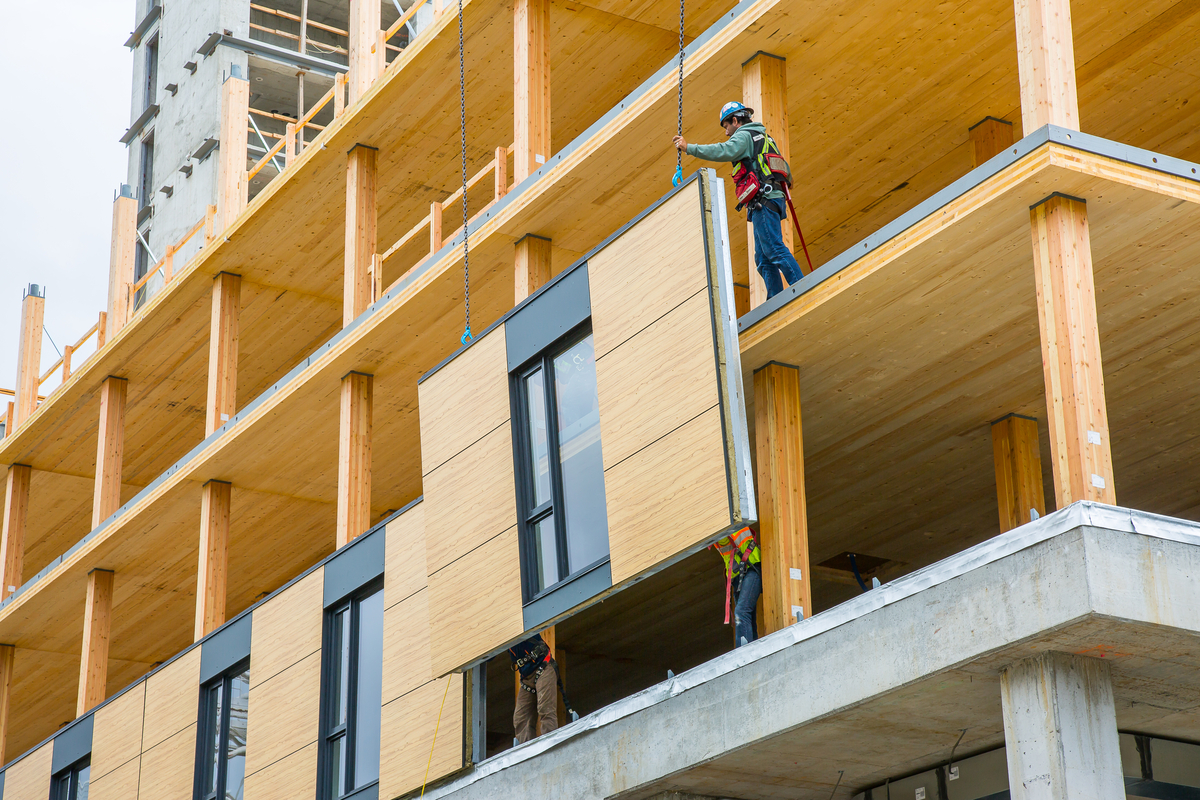
Le but de la dalle et poteau est de libérer des plateaux horizontaux. C’est le cas du système de dalle en bois lamellé-croisé (CLT) et poteaux en bois lamellé adopté pour la résidence d’étudiants Brock Commons, un immeuble de 18 étages de l’Université de Colombie-Britannique.
c. Panneaux
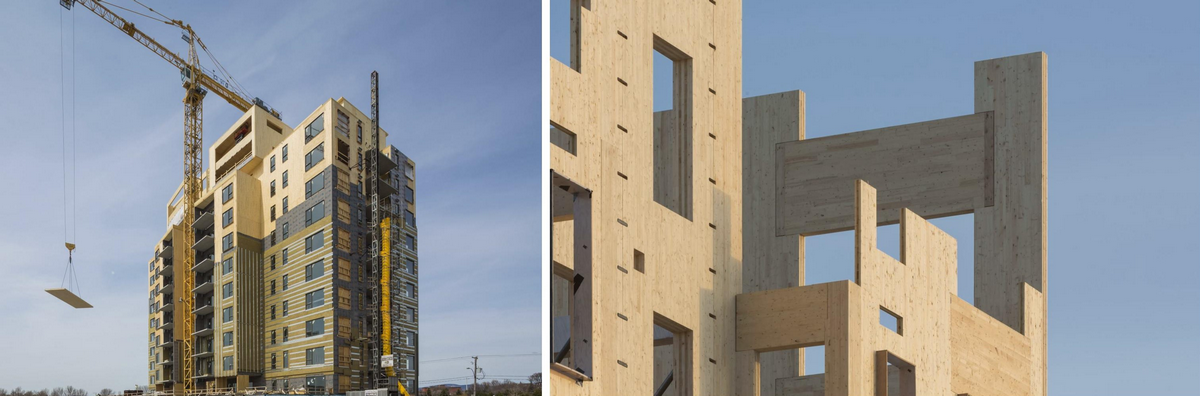
Projet Origine – Photos Stéphane Groleau.
Les panneaux impliquent une transmission directe des charges de l’axe horizontal à l’axe vertical, sans aucune forme de transfert. En conséquence, l’axe vertical génère un refend continu qui discipline la planification, mais l’habitation s’en accommode très bien en raison du grand nombre de cloisons requises. Le projet Origine à Québec illustre, sur une hauteur de 12 étages, le potentiel des panneaux en CLT produits par Nordic Structures, tout en incorporant occasionnellement des poutres afin de libérer de plus grands espaces.
d. Joint intégré
Constituant par lui-même un joint monolithe multidirectionnel, le joint intégré permet à la fois de simplifier le processus de jointement et de prendre des moments positifs : au lieu de réunir de 4 à 6 éléments (souvent très lourds) au même endroit, on les regroupe 2 par 2 en dehors du point de rencontre géométrique. Le système Componoform en est l’archétype.
II. Le Volume usiné – Environ 80 à 85 % du travail est réalisé en usine
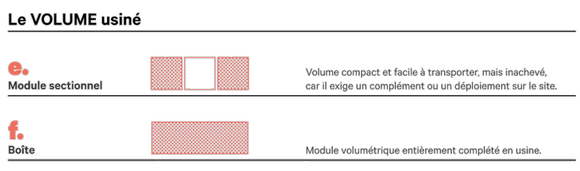
Le volume usiné implique que les espaces du bâtiment sont entièrement fabriqués, assemblés et finis à l’usine en tant que modules volumétriques ne nécessitant que de simples raccordements une fois sur le site.
e. Module sectionnel

Modules Holon de Broad Group (Chine).
Le module sectionnel demande quelques opérations faciles et rapides à réaliser sur le site en échange d’une réduction majeure du nombre de modules volumétriques à transporter. C’est ainsi que le module format double conteneur du système HOLON va déplier une paroi longitudinale à 90° pour l’appuyer sur un voisin similaire afin de doubler l’espace disponible. Tous les éléments structuraux sont en acier inoxydable et leurs jointements à sec permettent un démontage, une reconfiguration et même une relocalisation sans démolition.
F. Boîte
Ce sont surtout les modules volumétriques de type boîte qui permettent de maximiser la production usinée et de limiter le chantier à de simples raccordements entre modules et aux infrastructures. Évidemment, l’usine nécessite un investissement initial élevé, et donc une continuité de la demande afin d’amortir le tout.
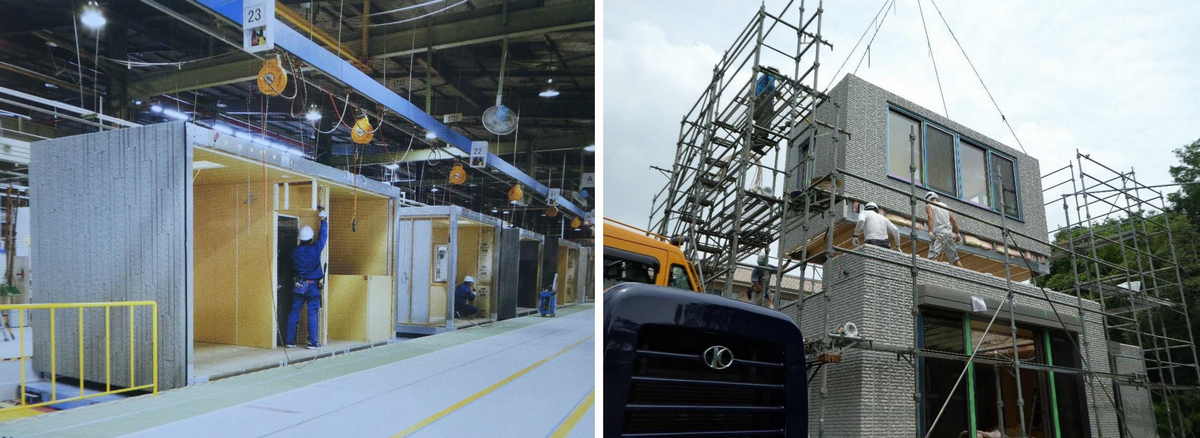
Assemblage et installation de modules Misawa Hybrid (Japon).
Depuis les années 1970, trois manufacturiers japonais produisent des modules volumétriques à ossature d’acier aux arêtes dont les dimensions sont similaires à celles d’un conteneur : Sekisui Heim, Misawa Hybrid et Toyota Housing. Leurs parois ouvertes agissent comme plateformes aux options sélectionnées par l’occupant et leur combinatoire fait en sorte qu’aucune maison n’est identique à une autre. Boulonnés entre eux en arrivant au chantier, ces modules peuvent être démontés en vue d’agrandir ou de réduire le bâtiment – voire même de le relocaliser.
- Les modules en bois d’ingénierie en Hollande
L’agence SeARCH a développé deux formules de boîtes en bois d’ingénierie. 1- Produits par De Groot Vroomshoop & Edgertdeboer, des modules à ossature aux arêtes en bois lamellé libérant les parois afin de générer de grands espaces pour l’école Klein à Amsterdam :
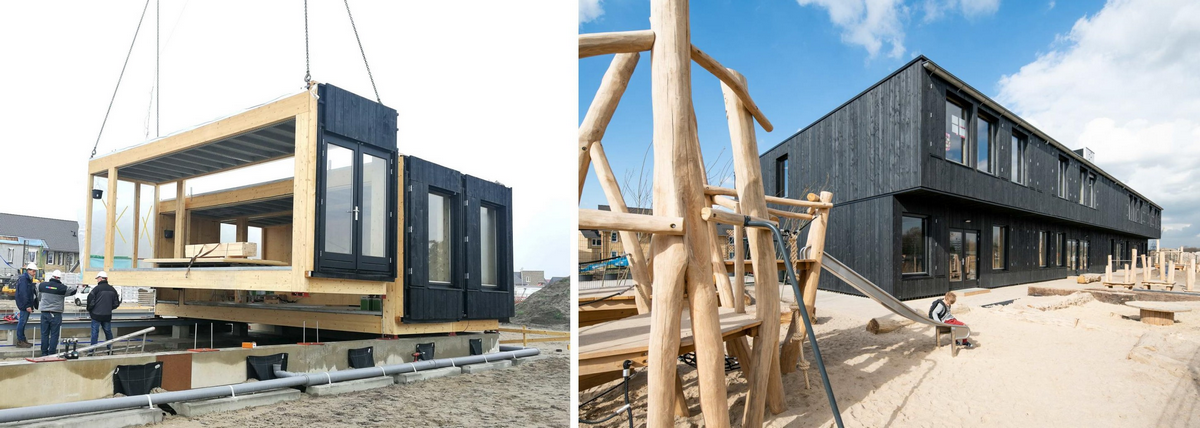
Et 2- Produits par Ursem Modulaire Bouwsystemen, des modules plancher en béton + murs-plafonds en CLT pour l’hôtel Jakarta, également situé à Amsterdam. Une série de niches en contrebas des murs de CLT permet de boulonner les tiges de raccordement émergeant du plancher :
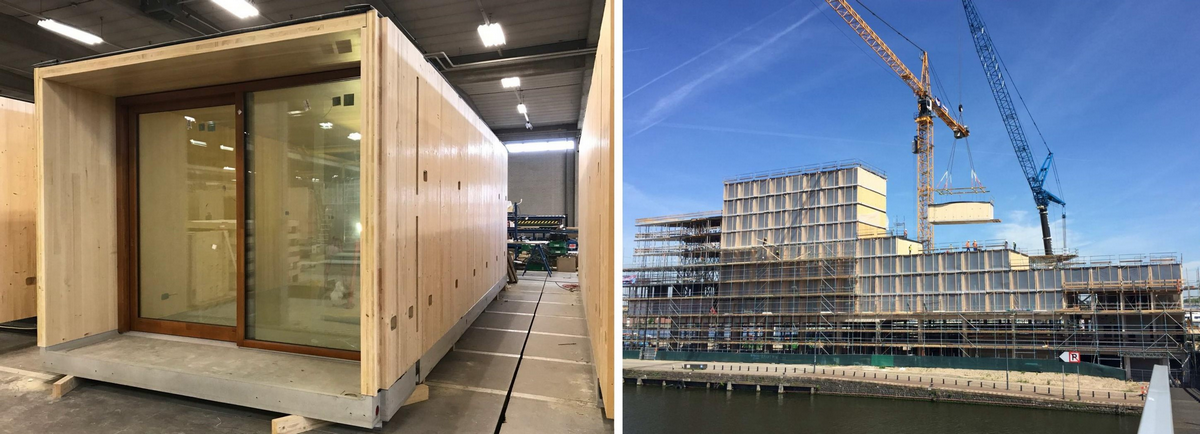
- Les boîtes mixtes au Royaume -Uni
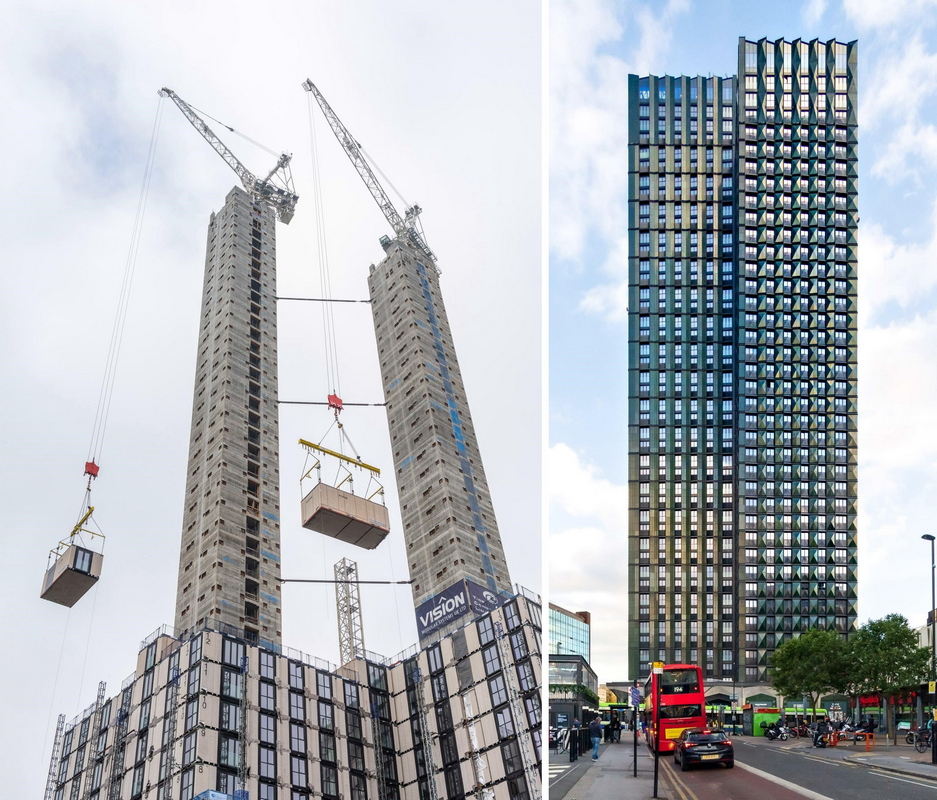
Édifices sur George Street à Croydon, TIDE Construction Limited et MJH Structural Engineers.
La plupart des boîtes produites au Royaume-Uni sont à ossature d’acier montée sur un plancher en béton, et plusieurs dépassent la trentaine d’étages. C’est le cas du double édifice érigé à Croydon, où les boîtes usinées chez Vision Modular Systems UK atteignent 38 et 44 étages.
- Le programme PPVC à Singapour
Le gouvernement de Singapour ne cède ses terrains qu’aux projets recourant à des systèmes certifiés « PPVC » (Prefinished Prefabricated Volumetric Construction) et la réglementation routière y permet des modules d’une largeur maximale de 3,5 mètres.
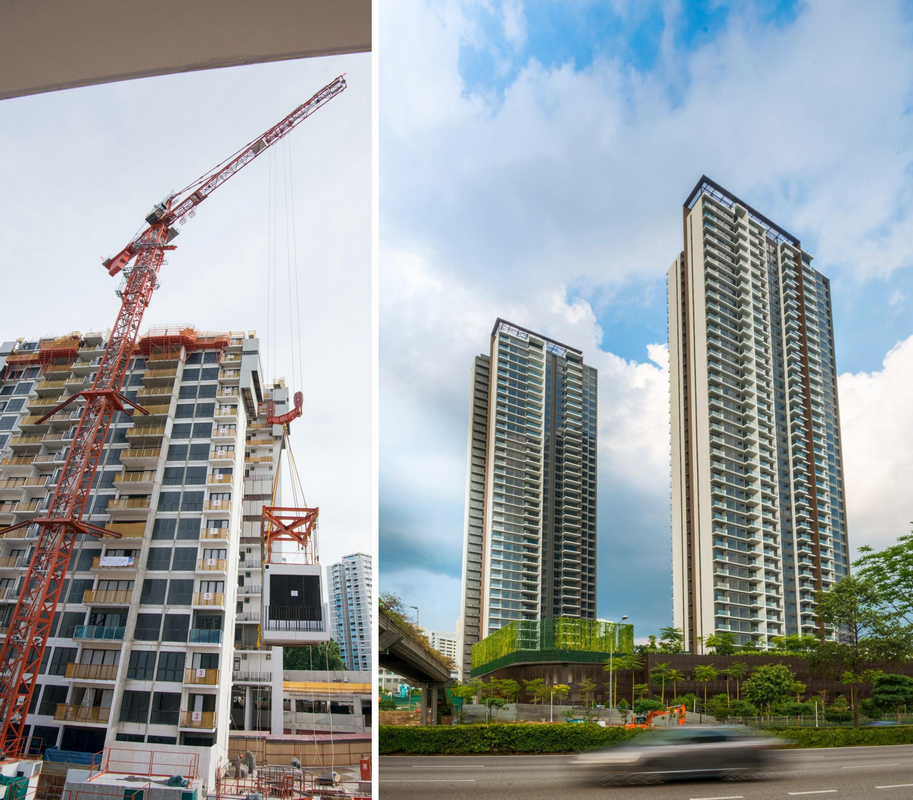
Les modules volumétriques préusinés en béton des tours jumelles de 40 étages du projet Clement Canopy (ADDP Architects) se limitent à ± 65 % de la superficie de chaque étage – cela est principalement dû au fait que les espaces de séjour dépassent la largeur de 3,5 mètres et sont donc coulés in situ.
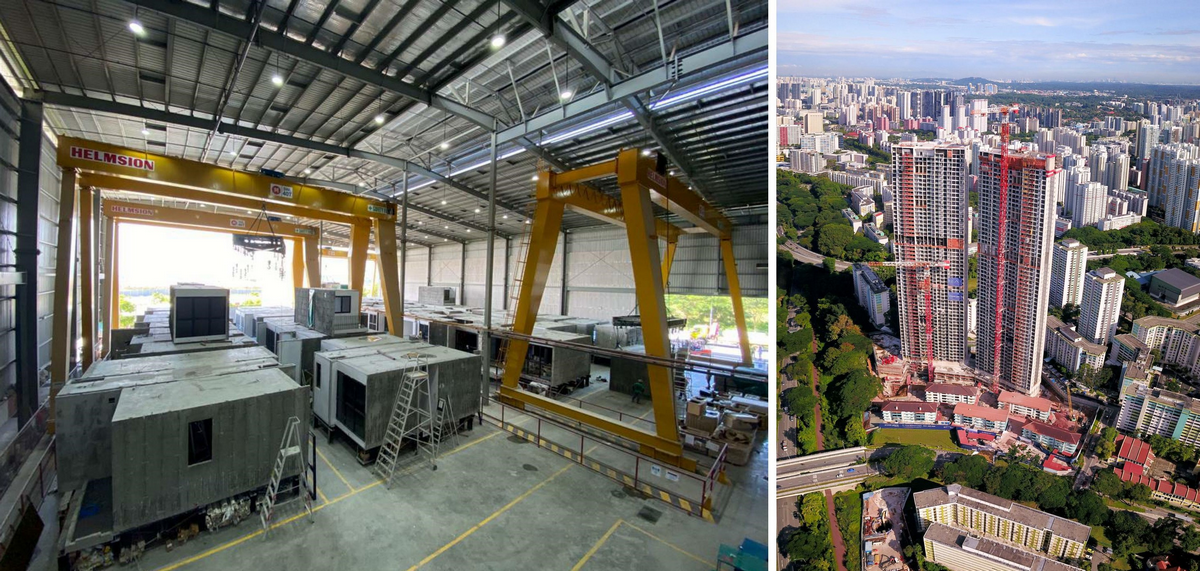
Ce sont également les architectes ADDP qui ont planifié les tours jumelles de 56 étages du projet Avenue South Residence, où les modules volumétriques préusinés en béton produits par United Tec Construction couvrent ± 85 % de la superficie de chaque étage, car ils incluent les espaces de séjour. Il s’agit des édifices à modules préusinés les plus élevés au monde présentement (juillet 2022).
- Le programme MiC à Hong Kong
Le gouvernement de Hong Kong préconise également des modules volumétriques en recourant à l’appellation « Modular Integrated Construction » (MiC), l’objectif étant de livrer annuellement 30 000 logements durant les vingt prochaines années. En raison du gabarit routier de Hong Kong, les modules sont limités à une largeur de 2,5 mètres.
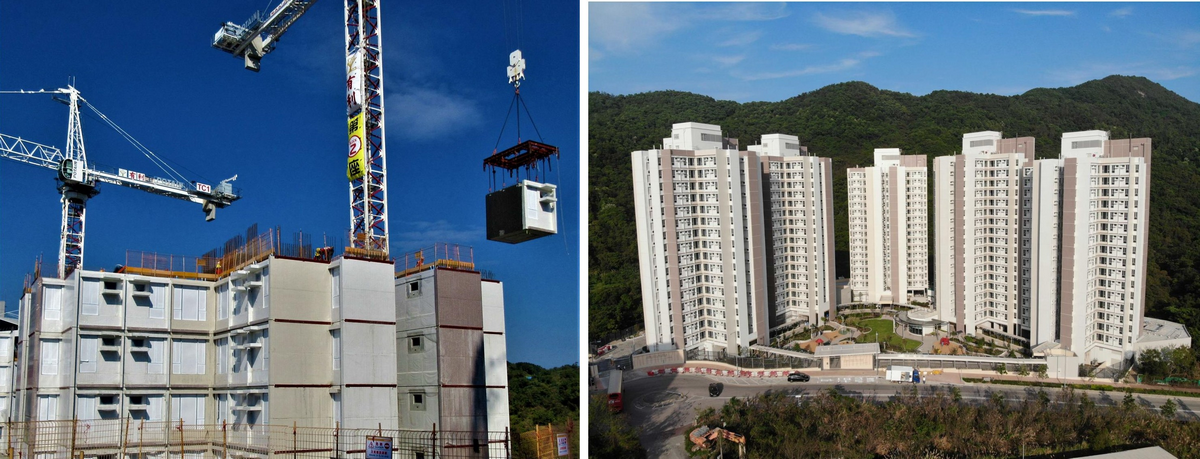
L’entreprise Yau Lee, à la fois manufacturier et entrepreneur général, y a récemment terminé les cinq édifices du projet Disciplined Service Quarters, qui totalisent 648 logements et où les modules 3D en béton préusiné couvrent ± 75 % de chaque étage.
III. L'hybride – Environ 70 à 75 % du travail est réalisé en usine
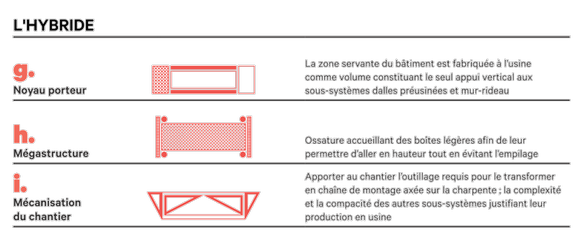
L’hybride vise le meilleur des deux mondes : compléter en usine les éléments sophistiqués du bâtiment et confier au chantier les opérations pénalisées par le transport.
G. Noyau porteur
Le noyau porteur propose un langage architectural basé sur la distinction entre espaces servants et espaces servis. Les espaces servants (cuisine, salle de bain, buanderie, escaliers, ascenseur, et al.) sont concentrés dans des noyaux volumétriques préusinés. Une fois sur le site, ces noyaux agissent comme seuls appuis verticaux à de grandes dalles et larges panneaux d’enveloppe destinés à accueillir les espaces servis (salon, salle à manger, chambres, et al.).
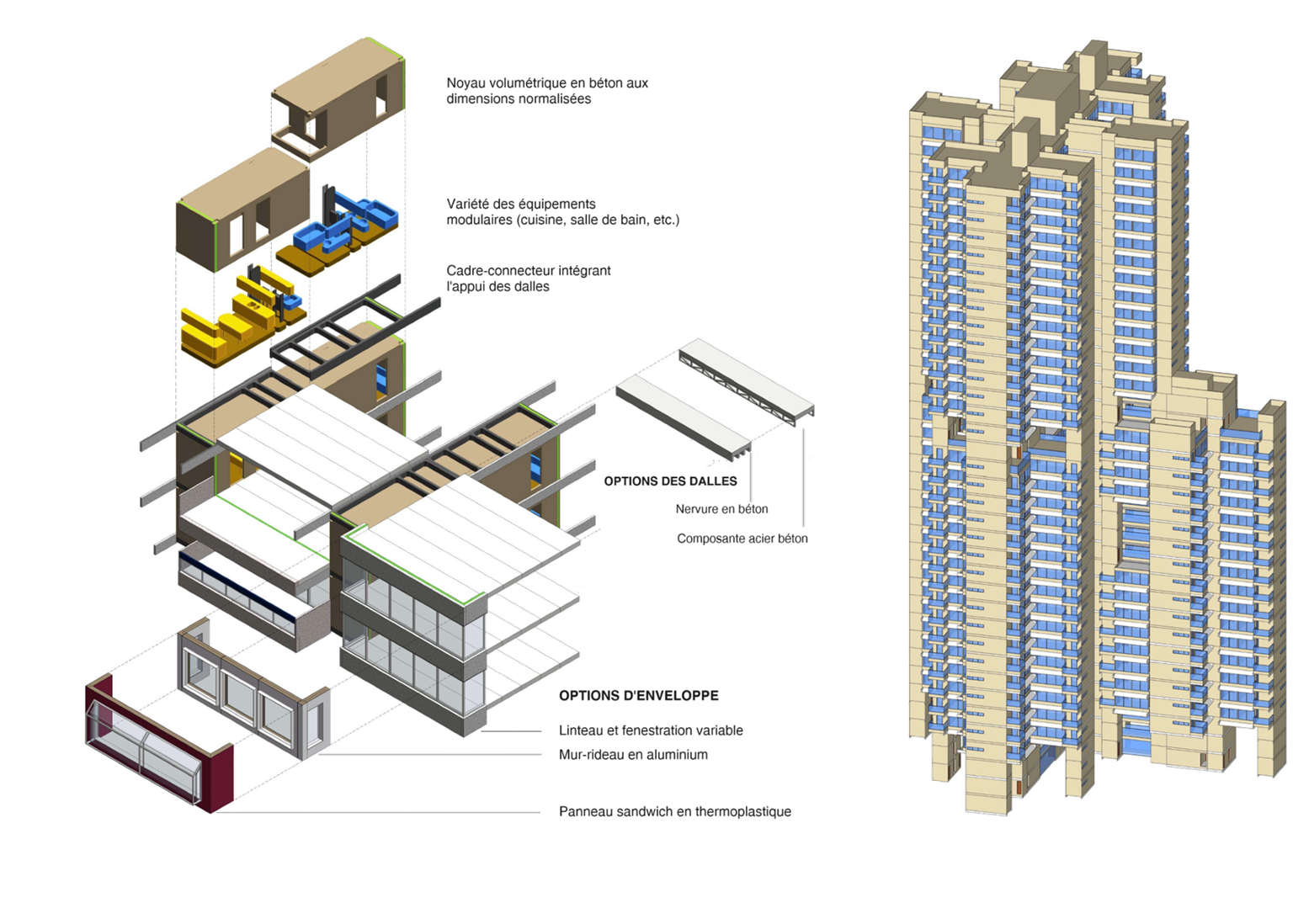
Le système de noyau porteur Richardesign, développé par l’auteur de ces lignes, offre une solution optimisée par rapport aux solutions de type boîtes :
• La superficie de l’édifice occupée par les noyaux correspond précisément à l’espace requis pour l’ensemble des services et équipements qu’ils intègrent, soit ± 30 à 35 % ; comme les modules d’un système de type « boîte » sont destinés à couvrir ± 80 à 85 % de l’édifice, la moitié d’entre eux ne transportent que de l’air !
• Les espaces servis d’une largeur de ± 6,0 à 7,2 mètres générés entre les noyaux offrent une grande souplesse à des variations de planification, ce que ne permet généralement pas le gabarit routier gouvernant la largeur de tout module volumétrique.
H. Mégastructure
.jpg)
Le but de la mégastructure est d’offrir des « étagères » où insérer des boîtes à charpente légère en vue de les approcher des centres urbains à forte densité. À Bergen (Norvège), la mégastructure en bois lamellé de l’édifice Treet permet à de telles boîtes d’atteindre une hauteur de 14 étages.
I. Mécanisation des chantiers
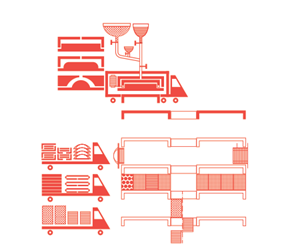
Distribution des sous-systèmes en mécanisation du chantier
La mécanisation du chantier répond à la logique de produire une charpente de béton in situ plutôt que d’en transporter les éléments pièce par pièce. Pour les autres sous-systèmes, elle recourt aux mêmes options que le Meccano assemblé au chantier.
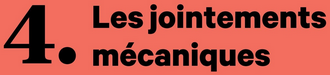
Tout système ou sous-système préusiné nécessite des jointements faciles et rapides à effectuer une fois parvenu sur le site afin de ne pas y compromettre les avantages économiques acquis en usine : ces jointements se doivent donc d’être mécaniques, c’est-à-dire à sec. De plus, une fois le chantier complété, ces jointements mécaniques permettront de modifier, voire de reconfigurer ou même de relocaliser, l’édifice sans destruction ni démolition, conformément à l’approche Design for Disassembly, c’est-à-dire DfD (C2C News, 2017).
Jointement boulonné
Alors que le jointement boulonné est pratique courante dans les structures préusinées en acier, des solutions fort ingénieuses sont disponibles en bois d’ingénierie et en béton préusiné. Le système en bois lamellé Shawood de Sekisui House (Japon) offre un véritable « Meccano » facile à monter : le dégagement de la perforation supérieure permet d’insérer rapidement le premier boulon, lequel va aligner les autres de facto.
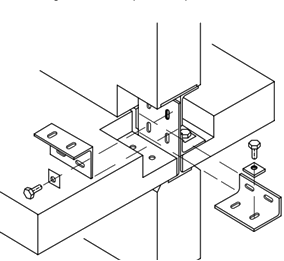
Connexions boulonnées en acier du système de panneau en béton Descon.
Enduits de lubrifiant, les boulons et fers angles à trous ovalisés du système Descon (Canada) sont nichés en retrait et protégés par un mortier ignifuge facile à concasser en cas de démontage.
Jointement par insertion
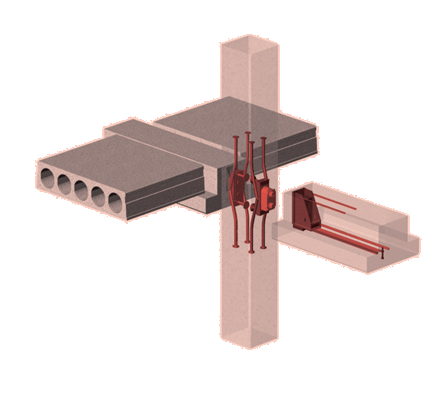
Connecteur Peiko (Filande).
Le recours à un collier en « U » permet de fixer rapidement la poutre dans un étrier intégré à la colonne.
Jointement par post-tension
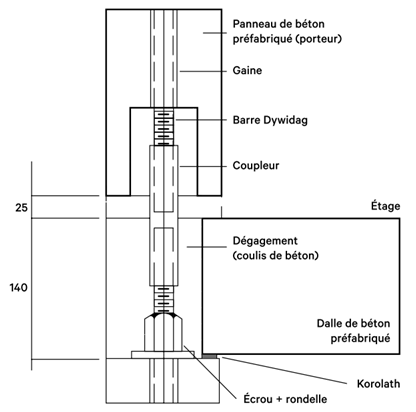
Jointement Dywidag, Sepp Firnkas Engineering (États-Unis).
La technologie de post-tension Dywidag engage le mur supérieur à appliquer, à la rencontre dalles + mur sous-jacent, une pression supérieure à tout effort latéral. Le démontage est possible, mais très lentement, afin de réduire progressivement la tension.
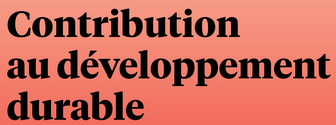
Même si les SCI offrent des avantages fonctionnels / technologiques / économiques significatifs, leur plus grand mérite réside dans leur quadruple contribution au développement durable : qualité, adaptabilité, réduction de CO2 et réduction des déchets.
Qualité
Deux facteurs assurent un haut degré de qualité :
- Assemblage rationalisé appuyé par un outillage de précision, accompagné d’un protocole de contrôle de qualité ;
- Recours à des détails uniformisés ayant démontré leur efficacité afin d’éviter les déficiences.
Adaptabilité
Les jointements mécaniques préconisés pour les SCI permettent les changements partiels, le démontage et même la relocalisation sans démolition, conformément aux prescriptions de l’approche DfD (Design for Disassembly) et aux objectifs de l’économie circulaire. Généralement, seul le calfeutrage est à refaire.
Réduction de l’émission de CO2
Plusieurs études internationales démontrent que la construction préusinée réduit les émissions de CO2 de l’ordre de 20 à 40 % par rapport à la construction en chantier. Le fait d’éliminer les coffrages sur multiples petits poteaux ainsi que les cohortes de camions ready mix y contribue sûrement en ce qui concerne la construction en béton coulé in situ.
Réduction de ± 50 % des déchets
Le recours à des composants modulaires et préusinés entraîne une réduction de ± 50 % des pertes de matériaux comparativement à la construction conventionnelle (Jaillon, Poon, et al., 2009). Comme démontré aux États-Unis par l’Environmental Protection Agency, c’est encore plus terrible lorsqu’il y a démolition : « […] demolition represented over 90 percent of total C&D debris generation. Construction, on the other hand, represented under 10 percent » (EPA, 2017)5.
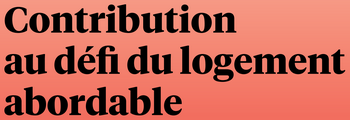
Il ne s’agit pas d’imposer les SCI à toutes les commandes architecturales, mais bien de rendre la qualité et l’adaptabilité abordables là où la quantité le permet, d’abord dans le domaine résidentiel où une crise majeure sévit à la grandeur de la planète.
Les Nations Unies prévoient que 3 milliards de personnes seront en quête d’un logement adéquat en 2030, soit 40 % de la population de la planète. Cela nécessite la production de 96 000 logements abordables chaque jour d’ici là, alors que 100 millions de personnes sont présentement sans logis (UN Habitat, 2022) ! Jusqu’à présent, seuls les procédés industrialisés capables de simplifier la production, tels que livrés par les SCI, sont en mesure de relever ce défi, tout en offrant une qualité supérieure au bas de gamme souvent emprunté par la construction traditionnelle afin de réduire les coûts.
C’est effectivement l’avantage ultime des stratégies et technologies de l’industrialisation : rendre le logement de qualité abordable pour tous.
Traduction
1 […] aucune industrie n’a fait pire… Dans son ensemble, ce secteur industriel est réticent à dépenser de l’argent sur des technologies, des logiciels de gestion de projet à la production de masse, qui ont révolutionné tant d’autres industries.
2 Les coûts des projets pourraient être réduits d’environ 30 % et les délais d’exécution raccourcis d’environ 40 % si les promoteurs avaient recours à l’ingénierie de la valeur (conception standardisée) et à des approches industrielles, comme l’assemblage de bâtiments à partir de composants préfabriqués hors site.
3 L’écosystème de la construction d’aujourd’hui
Le processus de construction est fortement axé sur les projets : il est élaboré à partir des spécifications uniques du client, à l’aide de conceptions créées de toutes pièces et avec un degré de répétition limité. La chaîne de valeur et les acteurs sont locaux et fortement fragmentés verticalement et horizontalement, ce qui entraîne une multitude d’intervenants impliqués à chaque étape et des frictions importantes sur le plan des interfaces. La construction est réalisée par des généralistes sur site, dans des environnements hostiles, et une grande partie de la main-d’œuvre est temporaire et manuelle.
L’écosystème de la construction du futur
Le processus de construction est de plus en plus axé sur les produits, ce qui signifie que les structures seront fabriquées hors site par des sociétés spécialisées. Les développeurs choisissent des conceptions entières ou des composants spécifiques dans une bibliothèque d’options développées en interne ou proposées sur le marché.
4 La DfMA est une méthodologie d’ingénierie qui se concentre sur la simplification de la conception d’un produit pour améliorer la facilité de fabrication et l’efficacité de l’assemblage (Siemens, 2020).
5 […] la démolition représente plus de 90 % de la production totale de débris. La construction, par contre, représente moins de 10 %.
Références
Richard, 2011: Richard, Roger-Bruno, Chapitre II-A FOUR STRATEGIES TO GENERATE INDIVIDUALISED BUILDINGS WITHIN MASS CUSTOMIZATION (p. 79-89) du volume « New Perspective in Industrialisation in Construction – A State of the Art Report » publié par le Task Group 57 du Conseil International du Bâtiment (CIB) et ETH Zurich, mai 2010, 329 p. https://www.irbnet.de/daten/iconda/CIB18177.pdf
Habraken, 1976: Habraken, N.J. (1976). Variations: The Systematic Design ofSupports, Laboratory of Architecture and Planning, M.I.T., Cambridge, Mass., U.S.A.
Richard, 2017 : Richard, Roger-Bruno, INDUSTRIALIZED BUILDING SYSTEM CATEGORIZATION, Premier chapitre de la Partie A du livre OFFSITE ARCHITECTURE : Constructing the Future, Routledge, New York, 2017, 281 p. https://www.taylorfrancis.com/books/e/9781315743332 (cf. « PREVIEW PDF »)
Jaillon, Poon, et al., 2009: Jaillon L, Poon C S, et al., THE EVOLUTION OF PREFABRICATED RESIDENTIAL BUILDING SYSTEMS IN HONG KONG: A review of the public and the private sector. Automation in Construction, 2009, 18(3): pp. 239-248. EPA, 2017: ADVANCING SUSTAINABLE MATERIALS MANAGEMENT:Facts and Figures Fact Sheet. United States Environmental Protection Agency (EPA), Washington, D.C., 2017, p. 18. https://www.epa.gov/sites/production/files/2019-11/documents/2017_facts_and_figures_fact_sheet_final.pdf