Des enjeux de taille
Toutefois, les projets rapides et peu dispendieux sont trop souvent synonymes de projets dévastateurs pour l’environnement. Par conséquent, en plus de penser à de nouvelles façons de livrer rapidement des logements abordables, on doit aussi réfléchir à la façon de réduire l’empreinte environnementale de ceux-ci. Le secteur de la construction accuse toutefois un retard en matière de productivité et d’innovation. L’industrie a eu du mal à faire évoluer ses approches comme l’ont fait d’autres industries au cours des dernières décennies, et la productivité en a donc souffert. Jumelé à une pénurie de main-d’œuvre, on observe ainsi un problème d’inefficacité sur les chantiers de construction, ce qui peut entraîner des retards ou des surcoûts dans les projets.
La construction industrialisée s’impose
La construction préfabriquée en bois s’impose comme une solution intéressante à ces enjeux. D’une part, le bois permet une réduction considérable des impacts environnementaux du secteur. C’est un matériau naturel renouvelable à faible empreinte environnementale. Local et abondant, il capture et stocke le carbone lors de sa croissance et il requiert peu d’énergie pour être transformé.
La préfabrication de sections de bâtiment permet, quant à elle, un gain majeur de productivité et de qualité de fabrication. Travailler en usine est synonyme de travailler dans un environnement contrôlé, à l’abri des intempéries, où l’accessibilité aux matériaux et aux outils est directe, les postes de travail sont ergonomiques et les processus de construction optimisés. Tous ces facteurs permettent des délais de construction plus courts et un produit final de qualité optimale.
Face à la croissance urbaine qui tend à promouvoir les bâtiments commerciaux et résidentiels de mi-hauteur, soit de cinq à huit étages, la préfabrication s’approprie la place qui lui revient. Les ingénieurs montrent cependant une certaine réticence à s’aventurer en hauteur avec des bâtiments discontinués puisque les solutions d’assemblage comportent certaines lacunes.
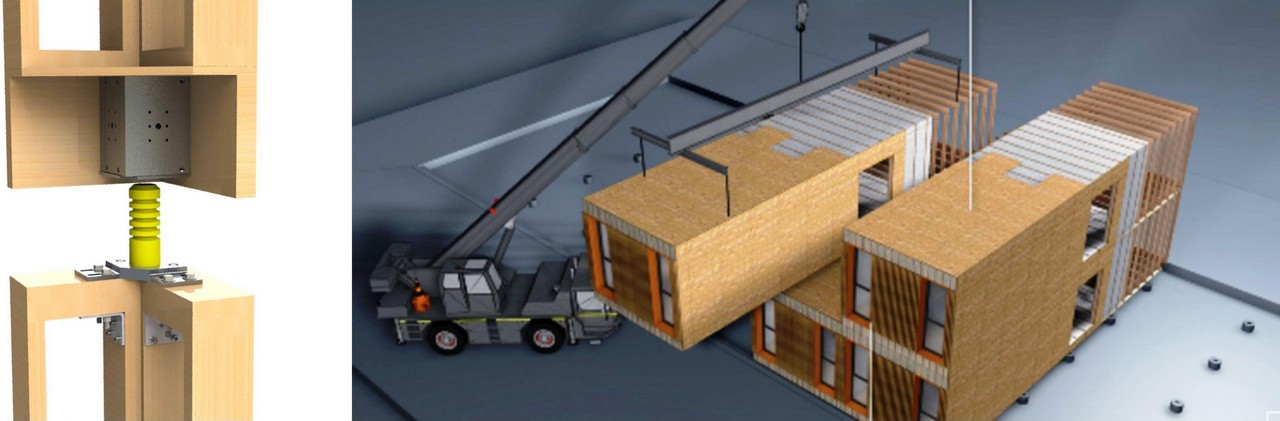
Concept de connecteur universel LOC. À l’assemblage, lorsque le module supérieur est déposé sur le module inférieur, des pièces mécaniques sont déplacées et déclenchent un système de verrou automatique qui maintient une liaison permanente entre les deux modules. – Source : CIRCERB
En effet, l’assemblage en chantier présente encore des défis, ce qui limite le niveau de préfabrication atteignable en usine. Les points de connexion entre les éléments préfabriqués doivent être laissés accessibles pour permettre leur assemblage au chantier. Les modules doivent donc arborer des murs inachevés lors de la sortie de l’usine puisque les connexions sont dissimulées dans la charpente. Ceci implique que des tâches de finition à l’intérieur des modules doivent être accomplies au chantier, ce qui nuit à la productivité du projet.
Le concept proposé
Pour augmenter les parts de marché des projets commerciaux et résidentiels de mi-hauteur par les préfabricateurs de la construction en bois québécois, l’industrie de la préfabrication aurait avantage à uniformiser et à standardiser ses méthodes d’assemblage des modules. L’utilisation d’un dispositif normé diminuerait substantiellement la réticence des ingénieurs concepteurs. C’est dans ce contexte qu’intervient le concept de connecteur universel pour les bâtiments préfabriqués que j’ai mis au point et breveté au cours de mes études de maîtrise et de doctorat en génie mécanique, à la Chaire industrielle de recherche sur la construction écoresponsable en bois (CIRCERB) de l’Université Laval. Ce dispositif de connexion LOC a été développé sous la supervision d’André Bégin-Drolet, professeur au Département de génie mécanique, et de Pierre Blanchet, professeur au Département des sciences du bois et de la forêt.
Ces connecteurs sont situés dans les coins des modules, à l’interface entre le plancher de l’étage et le plafond de l’étage inférieur. À l’assemblage, lorsque le module supérieur est déposé sur le module inférieur, des pièces mécaniques sont déplacées et déclenchent un système de verrou automatique qui maintient une liaison permanente entre les deux modules. La solution est donc 100 % mécanique.
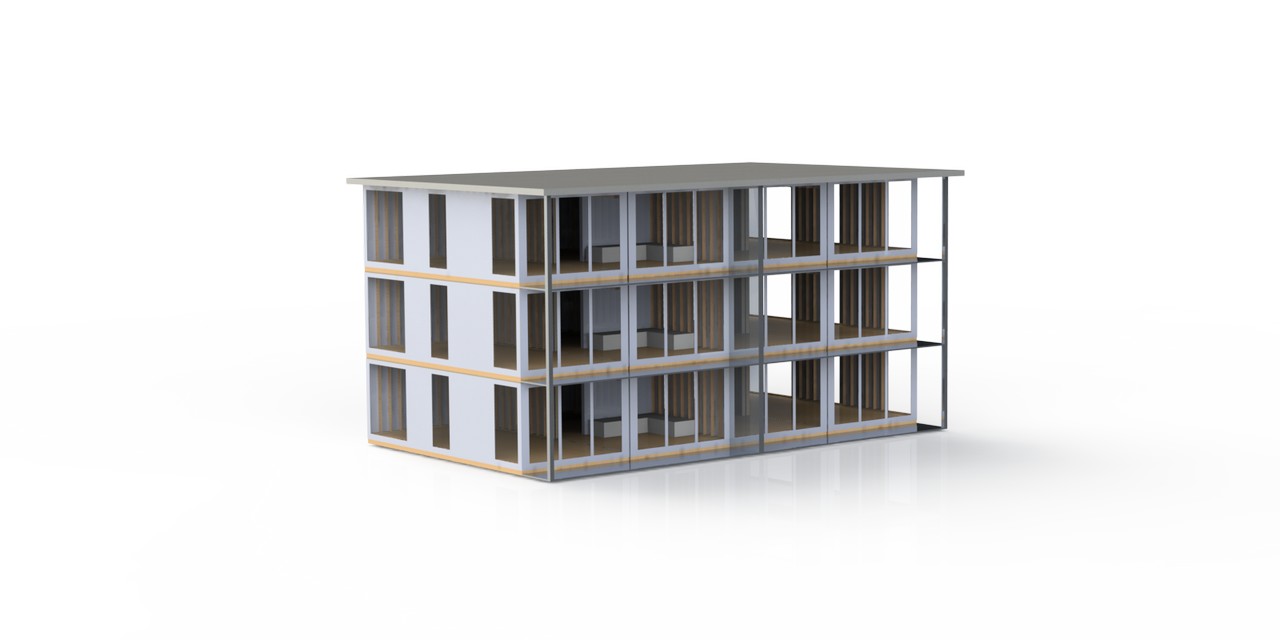
Le connecteur LOC reprend l’effet de tous les chargements que subit un bâtiment. Il permet le transfert des charges entre les modules et jusqu’aux fondations. – Source : CIRCERB
En plus de simplifier la connexion au chantier du fait de leur assemblage rapide et automatique, les connecteurs permettent la reprise des charges verticales (compression et tension) et des charges latérales (vent et séisme) que subissent les bâtiments. Ces connecteurs automatisés garantissent une stabilité et une intégrité structurales des bâtiments à système discontinués en ossature légère en bois. De plus, le recours à ces connecteurs réduit d’un facteur 4 le temps d’assemblage sur chantier et permet d’augmenter d’environ 25 % le niveau de finition des modules en usine.
Enfin, le connecteur universel pour modules préfabriqués en bois proposé s’avère une solution des plus prometteuses puisqu’il répond à des enjeux majeurs du secteur de la construction, soit le manque de productivité et de main-d’œuvre, ainsi que son lourd impact environnemental. Son utilisation augmente la rapidité au chantier et revalorise les avantages de la préfabrication modulaire. Étant donné les économies qu’il permet, il démocratise l’accès au logement.